The Duty of Welding Evaluation in Fighting Failures and Enhancing the Durability of Welded Frameworks and Components
Welding inspection is a vital element in the lifecycle of welded frameworks, functioning as a positive action against possible failings that can jeopardize safety and security and performance. By systematically determining defects such as porosity or insufficient fusion, examiners can substantially enhance the durability of critical parts. The application of diverse examination methods not just ensures compliance with sector standards but also cultivates a robust society of quality control. However, the effects of ignoring this important technique can be extensive, increasing inquiries regarding real impact on structural integrity and long-term performance. What are the best practices that can better boost examination effectiveness?
Relevance of Welding Examination
Welding examination functions as an essential guard in the honesty of welded structures, making sure that they satisfy rigorous safety and top quality standards. The relevance of this procedure can not be overstated, as it plays a crucial duty in determining potential issues before they intensify into tragic failings. By rigorously assessing welds, inspectors can confirm adherence to design specs and regulatory requirements, thereby alleviating risks related to structural compromise.
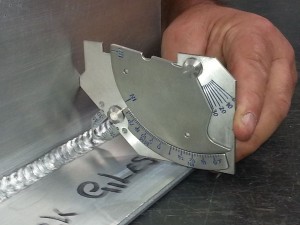
In addition, efficient welding examination improves the durability of parts, as it enables the early detection of problems that might cause wear and tear in time. This aggressive technique not only extends the life span of bonded structures but also promotes integrity and operational efficiency. In industries such as construction, aerospace, and vehicle, where security is paramount, the examination procedure is important.
Moreover, welding evaluation cultivates a culture of top quality assurance within organizations, encouraging adherence to best techniques and continual enhancement. By investing in detailed evaluation procedures, business can enhance their reputations and keep customer count on. Inevitably, the significance of welding evaluation hinges on its capability to promote safety and security, quality, and durability in bonded structures, making it an essential part of engineering stability.
Typical Welding Flaws
Numerous common welding flaws can jeopardize the stability of bonded frameworks, leading to prospective failings otherwise attended to. Among these issues, porosity is one of the most widespread, characterized by the visibility of small gas pockets caught within the weld metal. This can considerably deteriorate the joint, leading to reduced structural stability.

Another defect is insufficient blend, which takes place when the weld metal stops working to effectively fuse with the base product or previous weld layers. This lack of bonding can develop powerlessness that may fall short under anxiety. In a similar way, lack of infiltration describes insufficient depth of weld metal, protecting against the joint from achieving its designated toughness.
Fractures can likewise create throughout the welding process, typically as a result of rapid air conditioning or unacceptable welding parameters. These splits might propagate under tons, causing disastrous failings. In addition, extreme spatter can hinder the weld's quality by introducing contaminants.
Assessment Techniques and methods
Efficient evaluation techniques and techniques are vital for guaranteeing the integrity and longevity of welded frameworks. An extensive evaluation program utilizes a selection of non-destructive testing (NDT) approaches to identify potential flaws without jeopardizing the welded components. Amongst one of the most frequently used strategies are aesthetic assessment, ultrasonic testing, radiographic screening, magnetic fragment testing, and color penetrant testing.
Visual examination works as the initial line of defense, allowing inspectors to recognize surface area flaws such as splits, imbalances, or insufficient combination. Ultrasonic testing uses high-frequency acoustic waves to detect interior defects, supplying detailed information concerning the material's stability. Radiographic testing uses X-rays or gamma rays to visualize the inner structure of welds, allowing the identification of gaps and additions.
Magnetic fragment screening is reliable for discovering surface and near-surface suspensions in ferromagnetic materials, while color penetrant screening highlights surface-breaking flaws using tinted dyes. Each technique has its distinct benefits and constraints, demanding a strategic combination to achieve detailed evaluation protection. Applying these techniques systematically makes sure that any prospective concerns are determined early, fostering the reliability and longevity of bonded structures.
Influence on Structural Stability
The integrity of a structure is significantly influenced by the top quality of its welded joints, as they act as crucial factors of toughness and security. Improperly performed welds can result in stress concentrations, exhaustion failures, and eventually, catastrophic structural collapse. The dependence on welding as a primary ways of signing up with products demands extensive inspection protocols to make certain that welds fulfill established requirements and specs.
Shortages in weld quality, such as incomplete blend, fractures, or porosity, can endanger the mechanical residential or commercial properties of the joint, influencing load-bearing capability and general efficiency. When these issues go unseen, they can circulate under operational stress and anxieties, causing a decrease in structural stability over time. Regular and extensive examinations are crucial in recognizing these weaknesses before article they rise into significant failures.
In addition, the effect of ecological factors, such as deterioration, can be intensified by poor welding practices. Therefore, making sure premium welding with alert assessment not just promotes instant structural dependability however likewise extends the life span of components. Welding Inspection Milwaukee. Ultimately, the financial investment in proper welding inspection is an essential approach for protecting against structural failures, therefore enhancing the long life and security of welded structures
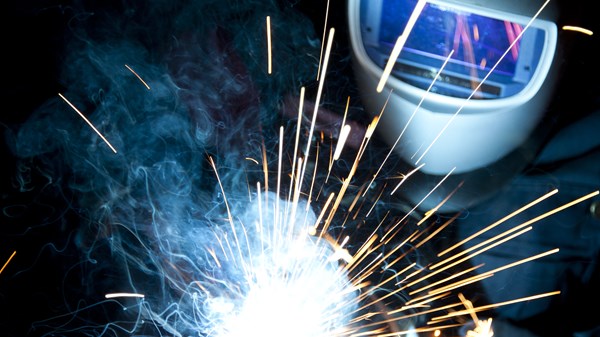
Finest Practices for Effective Inspection
Executing methodical examination methods is essential for making certain the integrity of bonded joints. Effective inspection begins with the advancement of detailed lists tailored to the particular welding processes and materials included. These lists must incorporate aesthetic inspections, non-destructive testing (NDT) methods, and documentation evaluation to make certain that all facets of the view it welding process are looked at.
Educating and accreditation of examination workers are vital parts of a successful evaluation program. Examiners must be skilled in different NDT methods, consisting of ultrasonic, radiographic, and magnetic fragment testing, to accurately determine defects such as splits, porosity, and insufficient blend.
Prompt inspections should be arranged at numerous stages of the welding process-- pre-weld, throughout welding, and post-weld-- to catch any prospective problems early. Additionally, maintaining thorough records of inspections promotes liability and helps with future analyses.
Final Thought
Welding evaluation is vital for identifying problems and ensuring the honesty of bonded structures. By using numerous assessment strategies, potential issues can be spotted early, therefore avoiding catastrophic failures and enhancing the durability of components. The application of ideal practices in inspection cultivates a society of quality control, guaranteeing compliance with layout specifications and regulatory criteria. Inevitably, effective welding inspection not only safeguards architectural honesty but likewise contributes substantially to the total dependability and sturdiness of bonded joints.
Welding inspection is an essential element in the lifecycle of bonded frameworks, offering as an aggressive measure against possible failings that look here can jeopardize safety and security and capability.Welding examination offers as a critical safeguard in the stability of bonded structures, ensuring that they fulfill rigorous safety and security and quality standards. Welding Inspection Milwaukee. Eventually, the significance of welding evaluation lies in its capability to maintain safety, high quality, and long life in welded structures, making it a fundamental element of design stability
Ultimately, the investment in proper welding assessment is a vital approach for guarding against architectural failures, thereby enhancing the durability and safety and security of bonded structures.
Welding examination is crucial for recognizing flaws and making sure the integrity of bonded frameworks. Welding Inspection Milwaukee.